Circuitry
Simple USB / Serial Communication with the CP2102N
Several years ago, a company called Future Technology Devices International (FTDI) sold what may have been the most popular USB / Serial converter on the market at the time, called the FT232R. But this post is not about the FT232R
, because that chip is now known for its sordid history. Year after year, FTDI enjoyed their successful chip’s market position – some would say that they rested too long on their laurels without innovating or reducing prices. Eventually, small microcontrollers advanced to the point where it was possible to program a cheap MCU to identify itself as an FT232R
chip and do the same work, so a number of manufacturers with questionable ethics did just that. FTDI took issue with the blatant counterfeiting, but they were unable to resolve their dispute through the legal system to their satisfaction, possibly because most of the counterfeiters were overseas and difficult to definitively trace down. Eventually, they had the bright idea of publishing a driver update which caused the counterfeit chips to stop working when they were plugged into a machine with the newest drivers.
FTDI may have technically been within their rights to do that, but it turned out to be a mistake as far as the market was concerned – as a business case study, this shows why you should not target your customers in retaliation for the actions of a 3rd party. Not many of FTDI’s customers were aware that they had counterfeit chips in their supply lines – many companies don’t even do their own purchasing of individual components – so companies around the world started to get unexpected angry calls from customers whose toy/media device/etc mysteriously stopped working after being plugged into a Windows machine. You might say that this (and the ensuing returns) left a bad taste in their mouths, so while FTDI has since recanted, a large vacuum opened up in the USB / Serial converter market almost overnight.
Okay, that might be a bit of a dramatized and biased take, but I don’t like it when companies abuse their market positions. Chips like the CH340
and CH330
were already entering the low end of the market with ultra-affordable and easy-to-assemble solutions, but I haven’t seen them much outside of Chinese boards, possibly due to a lack of multilingual documentation or availability from Western distributors. So at least in the US, the most popular successor to the FT232R
seems to have been Silicon Labs’ CP2102N
.
It’s nice to have a cheap-and-cheerful way to put a USB plug which speaks UART onto your microcontroller boards, so in this post, I’ll review how to make a simple USB / UART converter using the CP2102N
. The chip comes in 20-, 24-, and 28-pin variants – I’ll use the 24-pin one because it’s smaller than the 28-pin one and the 20-pin one looks like it has some weird corner pads that might be hard to solder. We’ll end up with a simple, small board that you can plug into a USB port to talk UART:
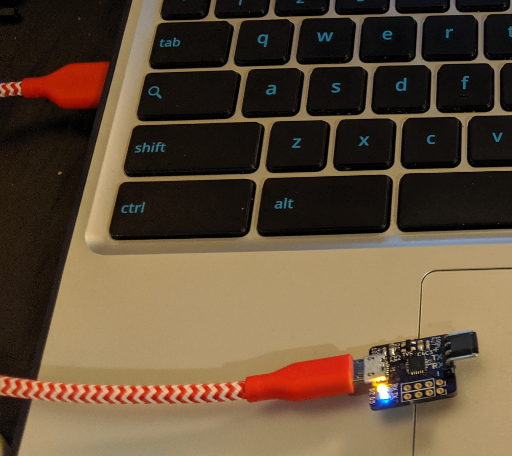
Drivers for the CP2102N are included in most popular OSes these days, including Linux distributions, so it’s mostly plug-and-play.
It’s worth noting that you can buy minimal CP2102N boards from AliExpress or TaoBao for about $1, but where’s the fun in that?
Making a Retro Wall Clock
It’s good to know what time it is, and once you work out how to use a RealTime Clock module, making a clock display seems like a natural next step. 7-segment LED displays used to be the go-to way to display time digitally before LCD and OLED screens got so cheap, and I thought it would be fun to make a more modern take on them with diffused multicolor LEDs for the actual lighting. I would like to write a post about drawing to traditional 7-segment digits using shift registers, but this project uses the easy-to-wire ‘Neopixels’ that we all know and love.
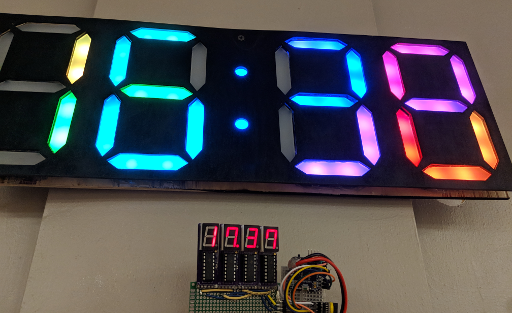
The one on the bottom doesn’t know about daylight savings, but you get the idea.
You’ll need a few materials for this project if you want to follow along:
- Access to a laser cutter and a 3D printer.
- About 6 x 12″ of 1/8″-thick ‘frosted’ acrylic, to diffuse the LEDs. (About 150 x 300mm, 3mm thick)
- Enough plywood to make a clock face for the front and back; I wound up using about 500 x 200mm each.
- 58 individually-addressable RGB LEDs. (28 sets of 2 for each segment of the 4 digits, and 2 more for the colon dots.)
- A DS3231 or similar realtime clock module.
- A microcontroller to run everything; I used an ATMega328 on an “Arduino” nano board to keep the code simple.
- Craft supplies: solder, soldering iron, glue, hot glue gun, wire, etc.
For the LEDs, I cut lengths off of a reel of LED strip that I ordered off Amazon; I think it used SK6812 LEDs and had 30 LEDs / meter. For the two dots of the colon, you can also buy small single-LED boards that are about 10mm in diameter and usually have WS2812B LEDs. I didn’t run into any problems stringing SK6812 and WS2812B LEDs together with Adafruit’s “Neopixel” library, but caveat emptor.
Recycling HDPE: What Doesn’t Work
Over the past month or two, I’ve been learning about plastic recycling with a friend at a local makerspace. We decided to start out with HDPE as a nice beginner’s material, because it melts at less than 200C and tends to be fairly nontoxic. We’ve tried a few different techniques now, and we’ve learned a lot about what doesn’t work.
This is an exciting field and we hope to make a decent press for forming 3mm and 6mm-thick HDPE sheets soon, but our early designs have shown us some key difficulties to be aware of if you are planning to start recycling plastics on your own. And I’ll mention this later, but please research what you plan to recycle ahead of time and avoid plastics which might release hazardous fumes. As you will see, I am not an expert.
Our first instinct was to imitate an injection-molding press, and we started by scavenging some large heating elements from a Goodwill-sourced griddle. It consisted of four ~13-Ohm coils arranged as two parallel banks, each consisting of two elements in series. That meant an effective resistance of 13 Ohms, or a bit over 9 amps at the mains 120V which it was more or less directly connected to.
We wound up clipping the heating coils out and scavenging some of the crimped and heat-insulated wiring, strapping them to a smooth-bore metal pipe, and then soldering or spot-welding the four coils back together in their original 2×2 arrangement. Temperature monitoring is all well and good, but this was a first attempt; we just wired the coils across a 2-prong plug, and flipped a surge suppressor on and off to control the heat. A handheld infrared thermometer gave us a rough indication of the tube’s temperature, and we aimed for 350-400F to melt the HDPE.
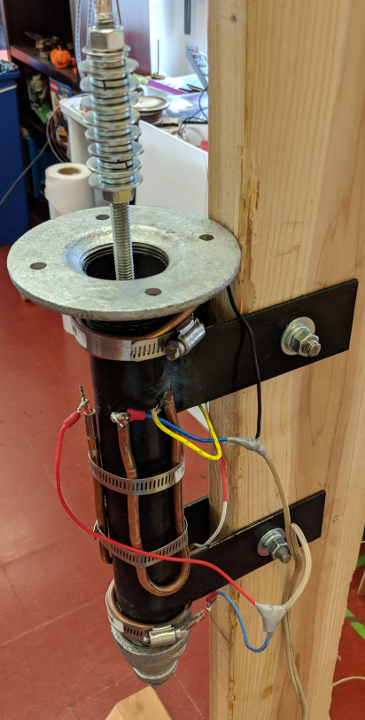
Our first attempt at a plastic-melting tube; the heating elements are the thick copper-coated wires, and the beige wires connect directly to a 2-prong wall plug.
The W1209: A (sometimes) STM8-based digital thermostat
Among the cheap gadgetry that constantly spews forth from the spawning pits of consumer electronics, sometimes you can find a gem. The W1209 is an interesting board which is designed to act as a thermostat which can also switch a relay when certain temperatures are reached. It is used in everything from rice cookers to yogurt machines to people who want their A/C to only turn on when it’s hot out. Originally they shipped with an aging but fairly capable STM8S003F3 microcontroller, and they cost less than $1.50 each.
Even so, their popularity has inspired the usual imperfect cloning process, so chances are that a board you buy from ebay, Aliexpress, Taobao, or Amazon today will need some touching up before you will be able to reprogram it. In this tutorial, we will replace the microcontroller and add a few missing capacitor/resistors. Then we’ll upload a simple test program to test that the microcontroller and board both work. So here is an example of what is probably the worst possible knock-off that you could fear to get, with missing or faulty parts highlighted:
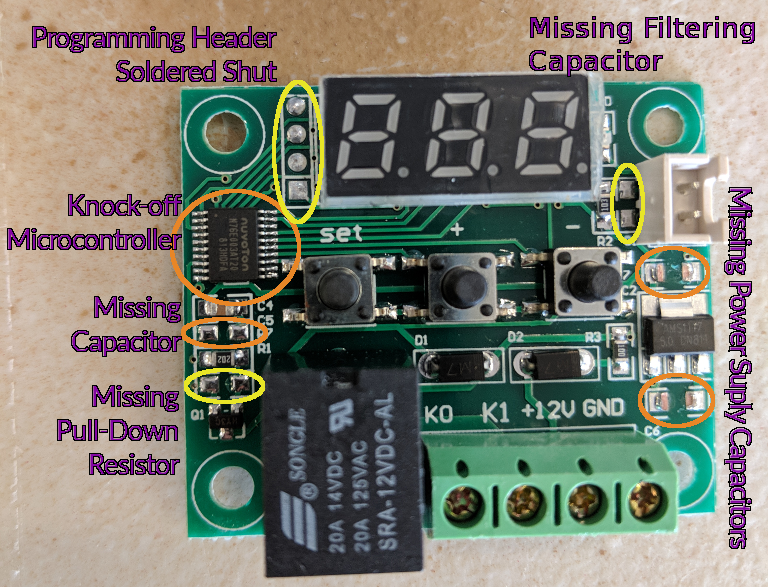
W1209 that needs fixing
Well, that’s life. You try your best, and then someone comes along and kicks you in the teeth. But let’s make some lemonade and take the opportunity to learn about fixing cheap-o knock-off circuit boards!
Your Own Hardware: Using KiCAD to Design a Minimal STM32 Development Board
It’s great to be able to write programs for a chip’s evaluation boards, but the real strength of microcontrollers is their ability to act as a low-cost, low-power “brain” for larger designs or products. And along those lines, I’ve been writing a few tutorials about bootstrapping some basic ‘bare metal’ STM32 projects using an STM32F031K6
“Nucleo” board sold by ST.
That’s a great way to get started and test ideas out, but what if you want to try your hand at building a robot, or a home automation widget, or some other sort of complex machine? It’s nice to avoid huge messes of breadboards and wires once you have a basic prototype working, and these days it only costs a few dollars to get a small custom circuit board manufactured. The catch is, they usually take a few weeks to arrive and you need to provide the design. Still, the boards that we design in this tutorial will cost less than $2 each.
In this tutorial, we will use a suite of free software called KiCAD to produce a small example board using the same basic STM32F031K6
chip that I’ve been writing programming examples for. Our board won’t be quite as nice as ST’s, and it will require an external USB device for programming and debugging. But on the other hand, our board will be smaller and cheaper, and you will be able to put the same design onto more holistic boards with other parts for your kickass robot or electronic vehicle or <insert dream here>:
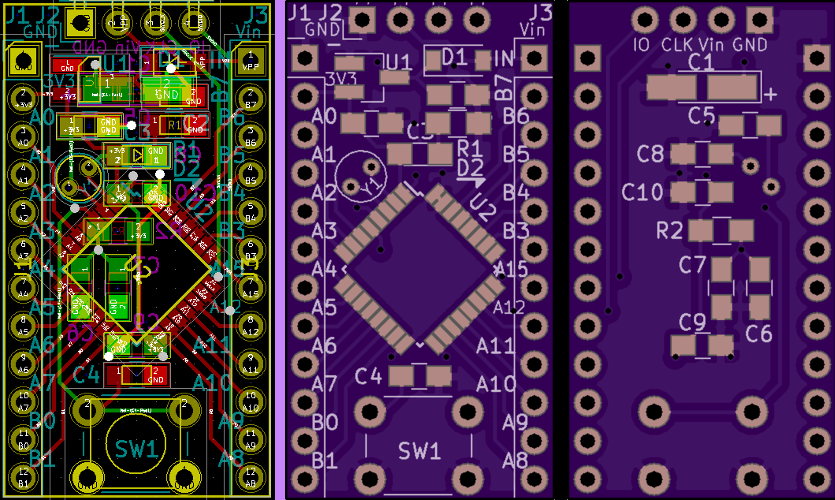
Left: A board like the one you’ll design in KiCAD. Right: OSHPark’s renders of the front and rear of the board.
The design files described in this post are all available in a Github repository, if you want a reference to follow along with.
DIY OLED Display Boards: SSD1306 and SSD1331
OLED displays are excellent solutions for low-power, high-visibility UIs that don’t need to depict much detail and can be smaller than a square-inch or two. These days, they are cheap and available enough to be viable options for the hobbyist:
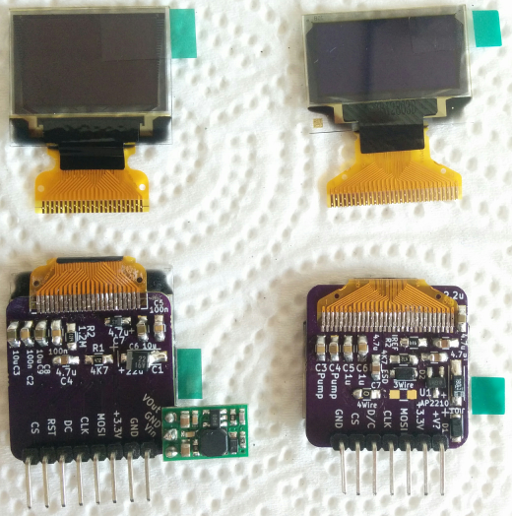
Top: The display panels as they arrive in the mail. Bottom: Boards with the circuits described in this post – the panels are glued to the other side.
These are two small display panels which you can find on Taobao, Alibaba, or eBay in small quantities for roughly $2-4 each. The one on the left is a 96×64-pixel SSD1331
16-bit color display. The one on the right is a 128×64-pixel SSD1306
monochrome display where each pixel is either ‘off’ or ‘on’ – typically ‘on’ is a white or blue color. Some of them have a row of 16px along the top set to yellow, but each pixel is still only one color.
In this post, we will walk through the circuitry (although not the code) required to control these displays using a microcontroller, including circuit schematics for laying out a ‘breakout board’ in your preferred EDA program – I used KiCAD, and I’ll also provide a link to those projects if you don’t want to design a new board.